Though we have truly not had much chance to work on the wood or leather any further (due to work pressures) I have made one significant addition to the project: I have acquired a working Becker Europa TG radio, the model that originally came with the car.
This was a fairly expensive optional extra, and I have never seen one in South Africa with original radio fitted (on the other hand, I almost never see fintails in the first place...). The radio is beautiful, over-the-top retro, and quite feature-rich: Station presets, and support for FM/AM and short-wave. It's a large, heavy (3kg) device, all metal, glass and tubes. Just another part of this car that is so wonderfully different to modern cars.
When the time comes nearer, I will have to find a suitable (original or other) speaker unit to hook up to the radio, and figure out in general how to get it working (RadioMuseum seems to be a useful resource). This radio is nothing like contemporary car radios - there are no friendly colour-coded or shaped plugs or labels on the rear, everything has to be soldered.
I have not taken pictures of the unit yet, will do so (and post them) once available. If anybody has further information regarding the general connection of this device, and a speaker, please give me a shout!
November 14, 2007
August 14, 2007
Slow going
We have not had much chance to work on the project over the past couple of weeks, but fear not, hopefully the next weekend will be filled with wood-stripping fun!
July 02, 2007
Restoring wood trim: Preparation
Though quite experimental at this stage, I have started to prepare the car's wood trim for refinishing. After very carefully disassembling the (many) wooden panels, bits, and pieces from the car, and labeling them, they are now stored in a big box.
Two types of wood trim was used in the interior:
Preparation
I chose a few small pieces to experiment on (a few solid trim pieces, and one thin piece of veneer form the dashboard, under the glove compartment). The aim was to completely remove all coating, readying it for re-coating. I used the following:
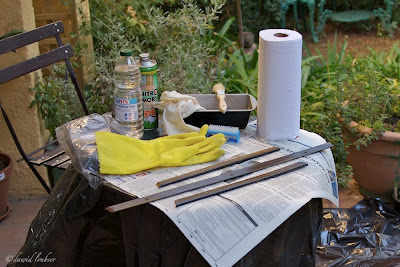

Solid Wood
Using a set of inserts from one of the windows as guinea pig, I applied a liberal coating of paint stripper (one one half only, to leave space for gripping each piece).

As per instructions, after waiting 5 minutes, I applied a second helping ("working" it into the toxic mush) and then leaving it for 20 minutes. After this, one is presented with an ugly sight (bye-bye 45 years of protective coating):

Using the plastic nail brush, I vigorously scrubbed the gunk off,
which easily removed most of the coating. On with the other half...

After this process, I thoroughly scrubbed the wood with steel wool and mineral turpentine, which is supposed to neutralise the paint stripper, and helped remove more of the stubborn coating. In many places, the coating penetrated (discoloured) the wood, so, using fine sandpaper, I sanded the wood until, after an great deal of effort (more then an hour per piece)
I ended up with a beautiful raw piece of wood (in this case, the dashboard radio insert) with a remarkably light colour:

Veneer
In order to ensure that my process does not damage the fine, very thin veneer of the dasboard, I used the small piece below the glove compartment (normally hidden underneath a chrome strip in anyway). Again, I applied NitroMors stripper to half of the piece.

To appreciate just how thin and delicate this veneer is compared to the thick layer of varnish coating, the following picture illustrates a high-magnification side view (and this illustrates how, in some places, the veneer has slightly separated - but not in any important areas). The coating is visible on top of the veneer, and this had to be removed without as much as scratching the veneer - sanding is definitely out.

After 20 minutes, the usual toxic gunk:

After scrubbing with a nail file, a thick rubbery layer of coating still remained - visible on the right (left side already completed for comparison):

This is where the ScotchBrite pad really worked wonders - it enabled me to remove the rubbery coating without any damage to the wood whatsoever, as the coating easily "peals" off - visible on the right (left side already completed for comparison):

Again, I scrubbed the veneer with steel wool and mineral turpentine. As can be see, the raw veneer is now exposed, and looking good (I was afraid the stripper or turpentine would warp, crack or dry it, but there seems to have been no ill effects):

Next Steps
The end result of a days' hard work is the completion of a few wooden pieces (which now appear very raw and dull, but "new"). Assuming the paint stripper leaves no long-term ill effects, the next steps are:
Two types of wood trim was used in the interior:
- Solid wood of a very light and fine grain, carefully hand-shaped to fit around the windscreen, all side windows, and on the door panels (twenty pieces in total). This wood has been stained/varnished to have a dark colour.
- Thin, triple-layered veneer on the dashboard, glove compartment and ashtray (five pieces in total). This wood already has a dark colour, and simply contains a thick layer of varnish for beauty and protection.
Preparation
I chose a few small pieces to experiment on (a few solid trim pieces, and one thin piece of veneer form the dashboard, under the glove compartment). The aim was to completely remove all coating, readying it for re-coating. I used the following:
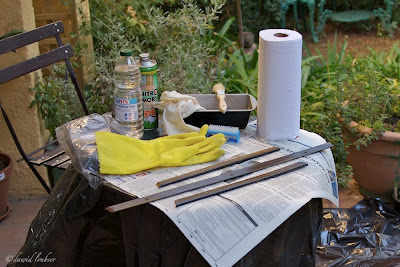
- NitroMors paint stripper, claims to be friendly to wood
- Thick latex gloves for protection against said paint stripper
- Breathing mask (ditto)
- Metal pan and brush to apply paint stripper
- Plastic nail brush
- Steel wool
- ScotchBrite scouring pad (rough texture)

Solid Wood
Using a set of inserts from one of the windows as guinea pig, I applied a liberal coating of paint stripper (one one half only, to leave space for gripping each piece).

As per instructions, after waiting 5 minutes, I applied a second helping ("working" it into the toxic mush) and then leaving it for 20 minutes. After this, one is presented with an ugly sight (bye-bye 45 years of protective coating):

Using the plastic nail brush, I vigorously scrubbed the gunk off,
which easily removed most of the coating. On with the other half...

After this process, I thoroughly scrubbed the wood with steel wool and mineral turpentine, which is supposed to neutralise the paint stripper, and helped remove more of the stubborn coating. In many places, the coating penetrated (discoloured) the wood, so, using fine sandpaper, I sanded the wood until, after an great deal of effort (more then an hour per piece)
I ended up with a beautiful raw piece of wood (in this case, the dashboard radio insert) with a remarkably light colour:

Veneer
In order to ensure that my process does not damage the fine, very thin veneer of the dasboard, I used the small piece below the glove compartment (normally hidden underneath a chrome strip in anyway). Again, I applied NitroMors stripper to half of the piece.

To appreciate just how thin and delicate this veneer is compared to the thick layer of varnish coating, the following picture illustrates a high-magnification side view (and this illustrates how, in some places, the veneer has slightly separated - but not in any important areas). The coating is visible on top of the veneer, and this had to be removed without as much as scratching the veneer - sanding is definitely out.

After 20 minutes, the usual toxic gunk:

After scrubbing with a nail file, a thick rubbery layer of coating still remained - visible on the right (left side already completed for comparison):

This is where the ScotchBrite pad really worked wonders - it enabled me to remove the rubbery coating without any damage to the wood whatsoever, as the coating easily "peals" off - visible on the right (left side already completed for comparison):

Again, I scrubbed the veneer with steel wool and mineral turpentine. As can be see, the raw veneer is now exposed, and looking good (I was afraid the stripper or turpentine would warp, crack or dry it, but there seems to have been no ill effects):

Next Steps
The end result of a days' hard work is the completion of a few wooden pieces (which now appear very raw and dull, but "new"). Assuming the paint stripper leaves no long-term ill effects, the next steps are:
- Bit by bit, complete all the wooden pieces (several months' patient work, I imagine)
- Determine the best process to result in beautiful dark, smooth wood trim encased in a thick layer of transparent coating. I imagine that brush-painting will not make this possible, so I will investigate spraypainting options.

June 28, 2007
Dashboard disassembly
Well, it took almost a whole day to disassemble the dashboard - now all that is left are the main electric harnesses, and the heating.

The dashboard is a fixed metal part of the chassis, and it is quite difficult to remove all the elements from within this framework. This is luckily counteracted by the overall simplicity of the car.
It was difficult to reach in everywhere to loosen the delicate chrome and wood panels, but by far the most difficult was to get in there and remove the instrument cluster. Most modern cars have simple electrical plugs that connect to the instrumentation, but in this case, several metal and copper pipes that physically convey water temperature and oil pressure had to be carefully loosened. The instrument cluster has the look and feel of a very old, delicate science instrument at the back, and you have to contort your arms and body into ridiculous positions to be able access the back of the cluster whilst still in position. I only found out later that I actually only had to loosen the one large retaining screw, as well as the main electrical plug, and that I could then pull the whole cluster out far enough in order to loosen the rest from the front
Interestingly enough, I had to physically remove the temperature gauge module from the instrument cluster, as it is connected to the engine with a single-piece metal pipe that cannot disconnect from the gauge itself (visible in the image above, wrapped in plastic for protection). But I fear for the day when I have to put the instrument cluster back together again!
I'm sure that the damaged soft vinyl covering of the dashboard could be repaired, but I'm just going to use the one from the other car, still in great condition. The wood, however, will be carefully re-finished.

The dashboard is a fixed metal part of the chassis, and it is quite difficult to remove all the elements from within this framework. This is luckily counteracted by the overall simplicity of the car.
It was difficult to reach in everywhere to loosen the delicate chrome and wood panels, but by far the most difficult was to get in there and remove the instrument cluster. Most modern cars have simple electrical plugs that connect to the instrumentation, but in this case, several metal and copper pipes that physically convey water temperature and oil pressure had to be carefully loosened. The instrument cluster has the look and feel of a very old, delicate science instrument at the back, and you have to contort your arms and body into ridiculous positions to be able access the back of the cluster whilst still in position. I only found out later that I actually only had to loosen the one large retaining screw, as well as the main electrical plug, and that I could then pull the whole cluster out far enough in order to loosen the rest from the front
Interestingly enough, I had to physically remove the temperature gauge module from the instrument cluster, as it is connected to the engine with a single-piece metal pipe that cannot disconnect from the gauge itself (visible in the image above, wrapped in plastic for protection). But I fear for the day when I have to put the instrument cluster back together again!
I'm sure that the damaged soft vinyl covering of the dashboard could be repaired, but I'm just going to use the one from the other car, still in great condition. The wood, however, will be carefully re-finished.
Project plan
Car restoration projects can easily become half-hearted, years-long affairs - some sad hulk of metal sitting in a back yard rusting away. Well not this project! I want to have the bulk of the work done in this year, which means I have about 6 months to accomplish this in. The goal of the project is to end up with an all-original, near-perfect car. The raw material is thus:
- My badly rusted but mechanically excellent 220b, currently registered in my name
- The newly acquired "donor car", a badly weatherbeaten but 100% original and complete, practically-rust-free 220Sb, which I legally bought, but for which there are no ownership papers available anywhere (which may turn into a bit of an administrative headache)
- Completely disassemble the 220Sb, starting with the interior.
- While starting to work on the wood and leather, get a quote to completely repaint and rust-treat the disassembled body.
- In the meantime, work week-ends on restoring the wood
- After the wood is done (after months of sweat and toil), work week-ends restoring the leather
- Once an acceptable quote is received, completely disassemble the rest of the car (with the help of Attie for the major mechanical components). This should be considerably less fiddly than disassembling the interiour.
- Send the car for painting
- While the car is being painted, start disassembling the mechanicals from the 220b, and upgrade the engine to 220Sb spec by transplanting the carburettors and intake manifold.
- When the car has been painted, assembly minimum required interiour components (i.e. driver's seat, steering wheel, basic electrics and windows) and then focus on the mechanical aspects of the car - suspension, engine and gearbox.
- Assemble and complete all electrics, lights, heating and ventilation, etc
- Assemble restored interior
The Leather Dilemma
I was under the impression that the cars that came out with real leather interior (versus the "MB Tex" vinyl) had seats with perforated panels, like the more modern Mercedes cars. This car, however, has a real blue leather interior that uses solid panels. It is, however, the original interior, and research has led me to believe that other people have seen this configuration as well.
This is the donor car before disassembly:

The seats (made of the most incredibly-thick blue leather) only show typical wear. The leather is not torn or punctured anywhere, but there are two challenges:
With careful disassembly, softening (re-humidifying) of the leather (likely using instructions I found in a very informative document produced for the Australian museum society), and hand-stitching them through the original stitching holes, I believe we will turn this interior into a beautiful one, without losing the charm of the original materials. This will be done after we refinish the wood, and I will document this in detail (hopefully helping somebody going through the same dilemma).
This is the donor car before disassembly:

The seats (made of the most incredibly-thick blue leather) only show typical wear. The leather is not torn or punctured anywhere, but there are two challenges:
- In places (such as the top of the rear seat) the leather has completely hardened from the sun, like carboard.
- The stitching that holds the panels together is completely brittle, and breaks even if you sit on it.
With careful disassembly, softening (re-humidifying) of the leather (likely using instructions I found in a very informative document produced for the Australian museum society), and hand-stitching them through the original stitching holes, I believe we will turn this interior into a beautiful one, without losing the charm of the original materials. This will be done after we refinish the wood, and I will document this in detail (hopefully helping somebody going through the same dilemma).
Build Quality
We have started to disassemble the interior of the car. I know this is a clichéd statement, but in doing this, I have realised again that the quality and attention to detail with which these cars have been put together is astounding. I have dis/assembled many cars in my life, and I have not once ever seen anything like the indestructible quality and thoughtfulness with which the components of these cars are put together.
This is an era which we will never re-live (not even a modern Bentley or a Rolls-Royce even approaches this quality) and when you consider the plasticised rubbish we have to put up with today ("better (i.e. more so-called features), faster, cheaper") it is such a gift to be able to see how it was done in the 1950s and 1960s.
My 1989 560SEC coupe, considered to be one of the best-built and most desirable "modern" Benz's before the downfall (the Daimler-Chrysler era of the 1990s and beyond) does not come close to this. It may be somewhat more refined and feature-rich (like the Starship Enterprise...), but it is not built like a W111.
I could ramble about the solid wood (not veneer or simulated wood) surrounds of all the windows (carefully inlaid and curved), the incredibly thick and plush leather, the carpeting that is thicker than that in my house, etc, but let me illustrate my point with one simple example: The corner air-vents.

Apart from being constructed from solid, polished cast metal (it really is quite heavy) they are fixed to the dashboard not using glue, plastic clips, screws or even bolts (even the latter two are unheard-of in most modern cars) but instead each has its own mechanism consisting a bracket and a spring to gently but firmly pull the vent to the dashboard from the rear, thereby not damaging the dashboard wood, making removal of the vent pipe easy, and for other reasons beyond me (since this is not a moving part).
This attention to detail is evident everywhere - and if they went to these lengths with something as silly as a dashboard vent, the mechanical excellence of these cars are self-evident. It was worth buying this donor car just for the pleasure of taking it apart!
(Handy tip: Buy a box of large-size Zip-Loc bags, and clearly label a bag for each significant set of parts. You don't want to throw the million-and-one interior parts into one big communal box, unless you want to do some serious treasure-hunting at re-assembly time)
This is an era which we will never re-live (not even a modern Bentley or a Rolls-Royce even approaches this quality) and when you consider the plasticised rubbish we have to put up with today ("better (i.e. more so-called features), faster, cheaper") it is such a gift to be able to see how it was done in the 1950s and 1960s.
My 1989 560SEC coupe, considered to be one of the best-built and most desirable "modern" Benz's before the downfall (the Daimler-Chrysler era of the 1990s and beyond) does not come close to this. It may be somewhat more refined and feature-rich (like the Starship Enterprise...), but it is not built like a W111.
I could ramble about the solid wood (not veneer or simulated wood) surrounds of all the windows (carefully inlaid and curved), the incredibly thick and plush leather, the carpeting that is thicker than that in my house, etc, but let me illustrate my point with one simple example: The corner air-vents.

Apart from being constructed from solid, polished cast metal (it really is quite heavy) they are fixed to the dashboard not using glue, plastic clips, screws or even bolts (even the latter two are unheard-of in most modern cars) but instead each has its own mechanism consisting a bracket and a spring to gently but firmly pull the vent to the dashboard from the rear, thereby not damaging the dashboard wood, making removal of the vent pipe easy, and for other reasons beyond me (since this is not a moving part).
This attention to detail is evident everywhere - and if they went to these lengths with something as silly as a dashboard vent, the mechanical excellence of these cars are self-evident. It was worth buying this donor car just for the pleasure of taking it apart!
(Handy tip: Buy a box of large-size Zip-Loc bags, and clearly label a bag for each significant set of parts. You don't want to throw the million-and-one interior parts into one big communal box, unless you want to do some serious treasure-hunting at re-assembly time)
Donor Car
My good friend and über-mercedes-mechanic Attie (from SDA Motors) has sold me the perfect donor car in order for us to start this restoration in earnest. While my 220b's body is very rusted, this car is weatherbeaten, but appears virtually rust-free, absolutely 100% complete (including every last interiour detail), and, best of all, it has never been laid a hand on. It has never been resprayed, it has never been disassembled. A fresh source of every part I could need, including a gorgeous complete interior just waiting for restoration. It still has engine and gearbox, but my current car's is likely to be far superior in lieu of all the time and money spent on it mechanically over the years.

For 45+ years of age, everything still looks remarkably well - the edges and door seams are still perfectly straight, and clicks shut like clockwork.

The only "problem" is that this is a model 220Sb, the more luxuriously-trimmed brother of my (rarer) 220b. The biggest difference lies in the more elaborate chrome and taillights (nicely explained by Martin's Heckflosse site) and I will have to decide on whether I want to keep the end-result a standard 220 (which will take some effort), or, if I use the donor car as the basis of this project, upgrade my current engine to "S" spec with the bigger Solex carburettors, etc.
Either way, the next step is the complete disassembly of the donor car, starting with the interior trim (which will likely be the most time-consuming to restore).

For 45+ years of age, everything still looks remarkably well - the edges and door seams are still perfectly straight, and clicks shut like clockwork.

The only "problem" is that this is a model 220Sb, the more luxuriously-trimmed brother of my (rarer) 220b. The biggest difference lies in the more elaborate chrome and taillights (nicely explained by Martin's Heckflosse site) and I will have to decide on whether I want to keep the end-result a standard 220 (which will take some effort), or, if I use the donor car as the basis of this project, upgrade my current engine to "S" spec with the bigger Solex carburettors, etc.
Either way, the next step is the complete disassembly of the donor car, starting with the interior trim (which will likely be the most time-consuming to restore).
June 15, 2007
Start of Project
Here she is: Blue Max - a pretty 1963 Mercedez-Benz "Fintail" model 220b (W111). I purchased the car in 2002 from a gentlemen who spent a great deal of money to semi-restore it to this state. I think he spent more on the engine than the actual complete worth of the car, and she drives beautifully. This car has never let me down, and I have had some great times with it (this was taken at God's Window in 2003).
.jpg)
This pretty car has several problems though:
.jpg)
This pretty car has several problems though:
- Though it doesn't look it (because of the fresh paint job done before I bought it) the car has a serious rust problem. Very serious. It spent part of its life in the hot, humid, salty Natal province.
- The pretty metallic pearl blue colour is not original, as metallic colours were only available upon request for the very expensive 300SE (W112) model.
- The interior heating never worked, the side vents are missing, so in my youthful ignorance I discreetly installed a very high-fidelity Infinity Kappa audio system, e.g. with the tweeters where the small side vents should be. In retrospect, ugh.
- My dear colleague and Managing Director decided to "reshape" the right rear door with his 280SE Mercedes, and it's so rusted it is not repairable (must be replaced).
Subscribe to:
Posts (Atom)